WHAT IS EGR?
EGR = Exhaust Gas Recirculation
A widely adopted route to reduce NOx emissions is Exhaust Gas Recirculation (EGR). This involves recirculating a controllable proportion of the engine's exhaust back into the intake air. A valve is usually used to control the flow of gas, and the valve may be closed completely if required.
The substitution of burnt gas (which takes no further part in combustion) for oxygen rich air reduces the proportion of the cylinder contents available for combustion. This causes a correspondingly lower heat release and peak cylinder temperature, and reduces the formation of NOx. The presence of an inert gas in the cylinder further limits the peak temperature (more than throttling alone in a spark ignition engine).
The gas to be recirculated may also be passed through an EGR cooler, which is usually of the air/water type. This reduces the temperature of the gas, which reduces the cylinder charge temperature when EGR is employed. This has two benefits- the reduction of charge temperature results in lower peak temperature, and the greater density of cooled EGR gas allows a higher proportion of EGR to be used. On a diesel engine the recirculated fraction may be as high as 50% under some operating conditions.
HISTORY OF EGR?
The first EGR systems were crude; some were as simple as an orifice jet between the exhaust and intake tracts which admitted exhaust to the intake tract whenever the engine was running. Difficult starting, rough idling, and reduced performance and fuel econom resulted. By 1973, an EGR valve controlled by manifold vacuum opened or closed to admit exhaust to the intake tract only under certain conditions. Control systems grew more sophisticated as automakers gained experience; Chrysler's "Coolant Controlled Exhaust Gas Recirculation" system of 1973 exemplified this evolution: a coolant temperature sensor blocked vacuum to the EGR valve until the engine reached normal operating temperature. This prevented driveability problems due to unnecessary exhaust induction; NOx forms under elevated temperature conditions generally not present with a cold engine.
Moreover, the EGR valve was controlled, in part, by vacuum drawn from the carburetor's venturi, which allowed more precise constraint of EGR flow to only those engine load conditions under which NOx is likely to form. Later, backpressure transducers were added to the EGR valve control to further tailor EGR flow to engine load conditions. Most modern engines now need exhaust gas recirculation to meet emissions standards. However, recent innovations have led to the development of engines that do not require them. The 3.6 Chrysler Pentastar engine is one example that does not require EGR.
HOW EGR WORKS?
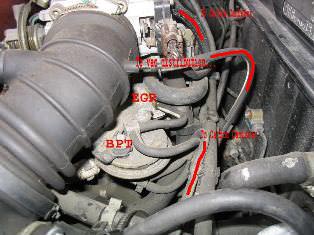
Usually, an engine recirculates exhaust gas by piping it from the exhaust manifold to the inlet manifold. This design is called external EGR. A control valve (EGR Valve) within the circuit regulates and times the gas flow. Some engines incorporate a camshaft with relatively large overlap during which both the intake valve and the exhaust valve are open, thus trapping exhaust gas within the cylinder by not fully expelling it during the exhaust stroke. A form of internal EGR is used in the rotary Atkinson cycle engine
EGR can also be implemented by using a variable geometry turbocharger (VGT) which uses variable inlet guide vanes to build sufficient backpressure in the exhaust manifold. For EGR to flow, a pressure difference is required across the intake and exhaust manifold and this is created by the VGT
EGR IN SPARK-IGNITED ENGINES?
In a typical automotive spark-ignited (SI) engine, 5 to 15 percent of the exhaust gas is routed back to the intake as EGR. The maximum quantity is limited by the requirement of the mixture to sustain a contiguous flame front during the combustion event; excessive EGR in poorly set up applications can cause misfires and partial burns. Although EGR does measurably slow combustion, this can largely be compensated for by advancing spark timing. The impact of EGR on engine efficiency largely depends on the specific engine design, and sometimes leads to a compromise between efficiency and NOx emissions. A properly operating EGR can theoretically increase the efficiency of gasoline engines via several mechanisms:
- Reduced throttling losses. The addition of inert exhaust gas into the intake system means that for a given power output, the throttle plate must be opened further, resulting in increased inlet manifold pressure and reduced throttling losses.
- Reduced heat rejection. Lowered peak combustion temperatures not only reduces NOx formation, it also reduces the loss of thermal energy to combustion chamber surfaces, leaving more available for conversion to mechanical work during the expansion stroke.
- Reduced chemical dissociation. The lower peak temperatures result in more of the released energy remaining as sensible energy near TDC (Top Dead-Center), rather than being bound up (early in the expansion stroke) in the dissociation of combustion products. This effect is minor compared to the first two.
- It also decreases the efficiency of gasoline engines via at least one more mechanism: Reduced specific heat ratio. A lean intake charge has a higher specific heat ratio than an EGR mixture. A reduction of specific heat ratio reduces the amount of energy that can be extracted by the piston.
EGR is typically not employed at high loads because it would reduce peak power output. This is because it reduces the intake charge density. EGR is also omitted at idle (low-speed, zero load) because it would cause unstable combustion, resulting in rough idle. The EGR valve also cools the exhaust valves and makes them last far longer (a very important benefit under light cruise conditions)
Since the EGR system recirculates a portion of exhaust gases, over time the valve can become clogged with carbon deposits that prevent it from operating properly. Clogged EGR valves can sometimes be cleaned, but replacement is necessary if the valve is faulty.
DIFFICULTIES WITH EGR?
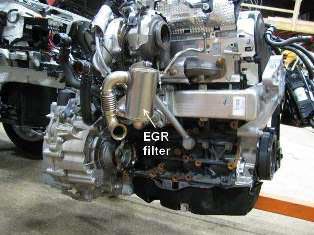
The deliberate reduction of the oxygen available in the cylinder will reduce the peak power available from the engine. For this reason the EGR is usually shut off when full power is demanded, so the EGR approach to controlling NOx fails in this situation.
The EGR valve can not respond instantly to changes in demand, and the exhaust gas takes time to flow around the EGR circuit. This makes the calibration of transient EGR behavior particularly complex- traditionally the EGR valve has been closed during transients and then re-opened once steady state is achieved. However, the spike in NOx / particulate associated with poor EGR control makes transient EGR behavior of interest.
The recirculated gas is normally introduced into the intake system before the intakes divide in a multi-cylinder engine. Despite this, perfect mixing of the gas is impossible to achieve at all engine speeds / loads and particularly during transient operation. For example poor EGR distribution cylinder-to-cylinder may result in one cylinder receiving too much EGR, causing high particulate emissions, while another cylinder receives too little, resulting in high NOx emissions from that cylinder.
Although the term EGR usually refers to deliberate, external EGR, there is also a level of internal EGR. This occurs because the residual combustion gas remaining in the cylinder at the end of the exhaust stroke is mixed with the incoming charge. There is therefore a proportion of internal EGR which must be taken into account when planning EGR strategies. The scavenging efficiency will vary with engine load, and in an engine fitted with variable valve timing a further parameter must be considered.
BENEFITS OF EGR REMOVAL?
Modern engines recirculate some of their exhaust gases back into the engine with the aim of reducing emissions.
This is the is the main benefit of the EGR system. The downside is that exhaust fumes containing carbon deposits are constantly being recirculated through the engine through time causing a build up of carbon deposits in the intake manifold etc.
These deposits sometimes contribute to the failure of the EGR system itself. Replacement EGR valves can be expensive and in the case of high mileage engines the continual carbon build up can eventually lead to total engine failure.
Removal of the EGR system by banking off the exhaust input and reprogramming of the engine managment ECU results in lowered engine temperatures, improved throttle response and economy and also can lengthen engine life by reducing oil contamination and carbon deposits.
EGR IN DIESEL ENGINES?
By feeding the lower oxygen exhaust gas into the intake, diesel EGR systems lower combustion temperature, reducing emissions of NOx. This makes combustion less efficient, compromising economy and power. The normally "dry" intake system of a diesel engine is now subject to fouling from soot, unburned fuel and oil in the EGR bleed, which has little effect on airflow but can cause problems with components such as swirl flaps, where fitted. Diesel EGR also increases soot production, though this was masked in the US by the simultaneous introduction of diesel particulate filters. EGR systems can also add abrasive contaminants and increase engine oil acidity, which in turn can reduce engine longevity.
Though engine manufacturers have refused to release details of the effect of EGR on fuel economy, the EPA regulations of 2002 that led to the introduction of cooled EGR were associated with a 3% drop in engine efficiency, bucking a trend of a .5% a year increase
Contact Details
HalstockYeovil
Somerset
BA22 9SY 01935 891616 07920 523676 sales@geraldhallettlandrover.com